一个小小改善,把行业30年的生产模式给改变了,不仅仅效率提高了,还能每年节省上千万元!更为重点是通过这种模式让员工知道,任何一个改善都有可能是一种革命性的变化和收益!
改善背景:
某药业公司车间结果在进行精益管理流程分析过程中发现压丸工序是效率的瓶颈,因此在睿信咨询的咨询团队的指导下进行问题的解决。
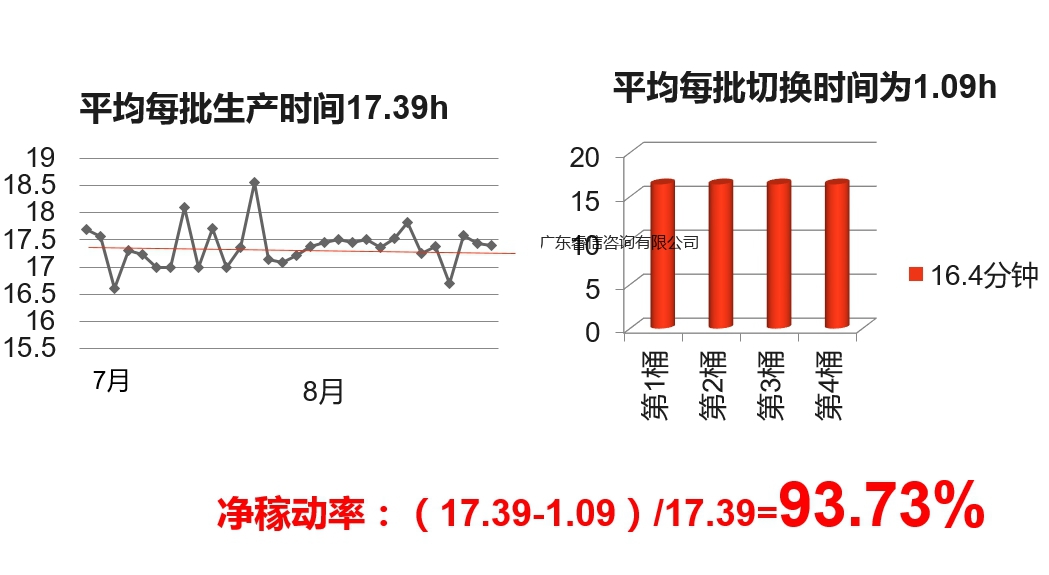
通过对稼动率的分析发现,批次之间的转换是瓶颈的重点来源。
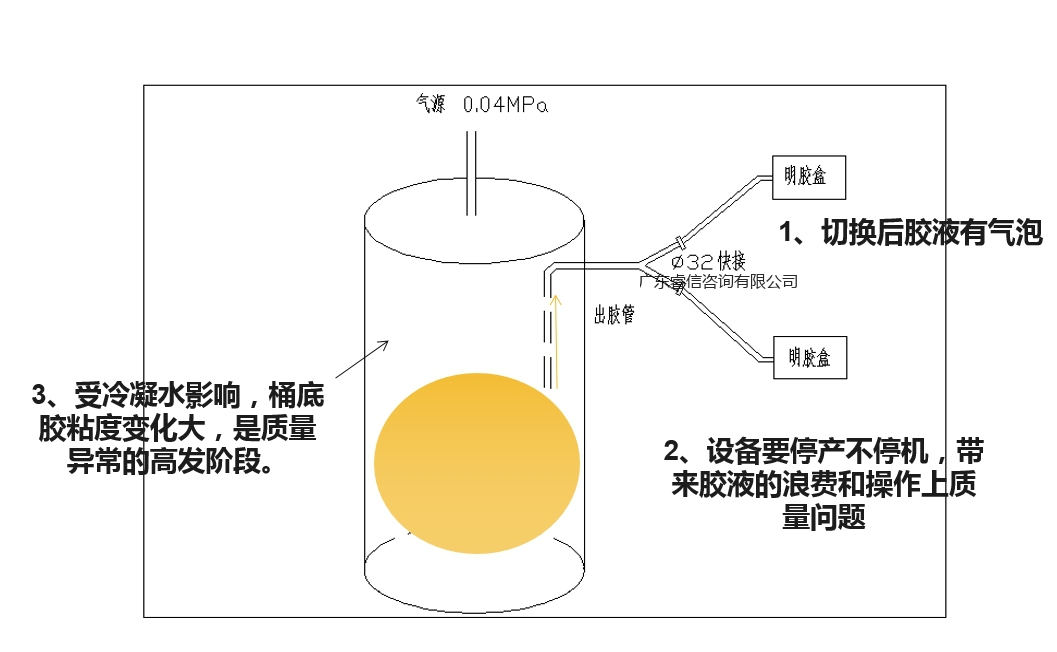
再往下深究发现,切换过程胶液的气泡产生导致时间浪费的重点原因。这个问题据说是传统软包压丸的30年的传统做法!一直没有人去改变!
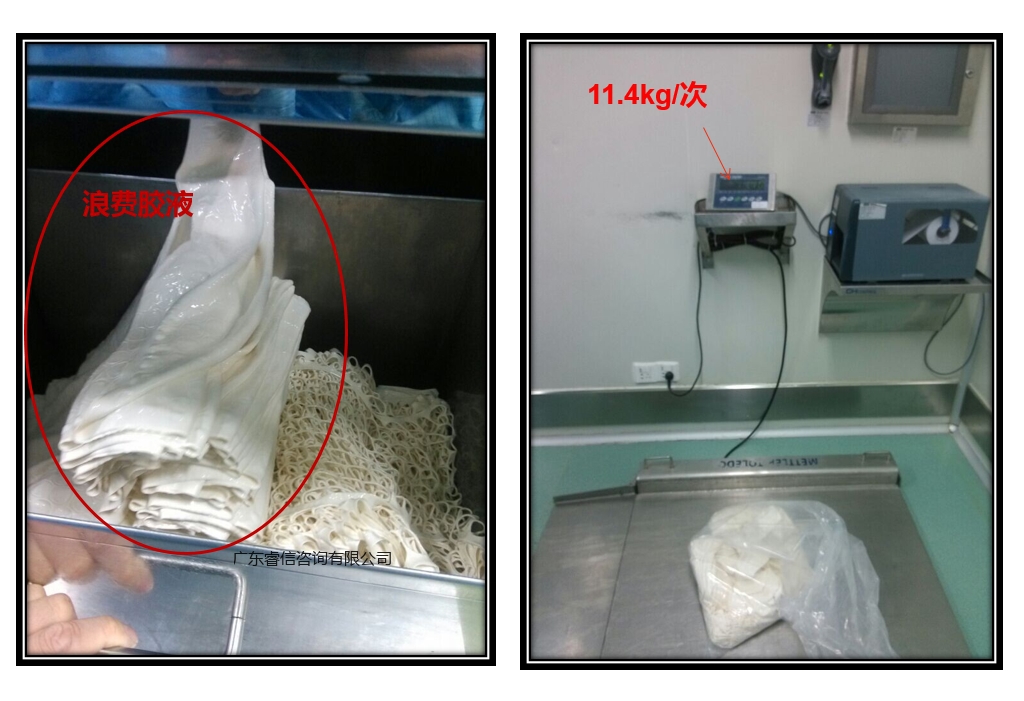
这种生产模式还会造成大量的胶液浪费!
通过一系列的改造,气泡的产生问题得到了最终完美解决。单台机器的节约成本保守估计每年节约145万,其他产线机器综合计算每年至少节约700万!